UK’s biggest opportunity from battery waste is to feed its cathode manufacturing industry
-
Re-processing scrap from the scale up of UK gigafactories could generate up to 20,000 tonnes of cathode active materials that can be reused, capable of making 7GWh of new batteries, equivalent to 100,000 cars.
-
By 2040 recycled battery waste from end-of-life vehicles could supply enough cathode materials to produce 60GWh of new batteries.
-
Cathode active materials make up ~50% of the total cell cost, containing critical metals that can be harvested from production scrap and retired batteries.
-
Battery producers can build a viable circular value chain to benefit from recycled material feedstock. These can be produced at a lower carbon footprint than mined materials.
-
The EU Battery Regulation proposes that from 2030, all new batteries must contain 4% Nickel, 12% Cobalt and 4% Lithium, by weight, from recycled materials, with higher targets from 2035.
-
Cathode active material suppliers are well placed to deliver battery quality materials from waste by working closely with recyclers and harnessing material recovery technologies like hydrometallurgy* and direct recycling**.
Batteries of the future need large quantities of Nickel, Lithium and other materials to supply the growing electric vehicle (EV) market.
Recovering battery materials is critical to making new batteries and can be produced at a lower carbon footprint than mined materials. Battery producers can build viable circular eco-systems to harness the manufacturing scrap to build new cells.
The Advanced Propulsion Centre (APC) calculates that manufacturing scrap from the scale up of UK gigafactories could generate up to 20,000 tonnes of cathode active material (CAM) that can be reused, based on UK production capacity reaching 90 GWh by 2030 [see Demand for gigafactories in the UK].
In addition, when you include vehicles that have come to their end-of-life (EoL), it’s estimated 28,000 tonnes of battery waste could be reusable. So there are real opportunities to recover critical battery materials from recycling (see graph below).
When we get to 2040, EoL vehicles will make up the majority of the battery waste, totalling 235,000 tonnes from vehicles and production sites in the UK (see graph below). This could supply enough CAM metals to produce 60GWh of new batteries. Strategic recovery of these materials is key to a sustainable and net-zero focused EV industry.
Cathode active materials make up 40-50% of the total cell cost, depending on cell chemistries. Metals like Nickel, Cobalt and Lithium can be recovered from processed scrap local to the plant, saving on logistic costs and creating supply circularity and environmental benefits.
How does the EU Battery Regulation impact production and recycling?
In the future, recycled materials will be even more important to battery producers. The recently announced EU Battery Regulation proposes all new batteries sold in Europe from 2030 must meet the minimum threshold of 4% Nickel, 12% Cobalt & 4% Lithium, by weight, of recycled materials. Higher are thresholds are planned from 2035.
With EV batteries lasting more than 10 years on most vehicles, the supply of retired batteries is limited in the ramp up of EV adoption to 2035. This constrains the amount of recycled metals available from EoL vehicles alone in the short term. The above recycled content thresholds seem achievable if the EU Battery Regulation accommodates battery production scrap as well as end-of-life batteries.
NOTE: These figures are based on EoL retirements and battery production in the UK. We expect the situation to be similar across the whole of Europe.
To close the circular economy loop, local CAM manufacturing is key. It would further help to make the UK automotive and battery industry sustainable, both from an environmental and economical perspective. These are key objectives of the APC and Automotive Transformation Fund (ATF).
* Hydrometallurgy is the process of extracting metals using liquid processes (as opposed to pyromethallurgy which involves high temperatures). Hydrometallurgy has been shown to enable recovery of more of the cathode active materials than thermal processing.
** Direct recycling involves removing and reusing components in such a way that they can be reused without the need for further complex processing.
Published: 03/02/2022
UK’s biggest opportunity from battery waste is to feed its cathode manufacturing industry
Recovering battery materials is critical to making new batteries and can be produced at a lower carbon footprint than mined materials.
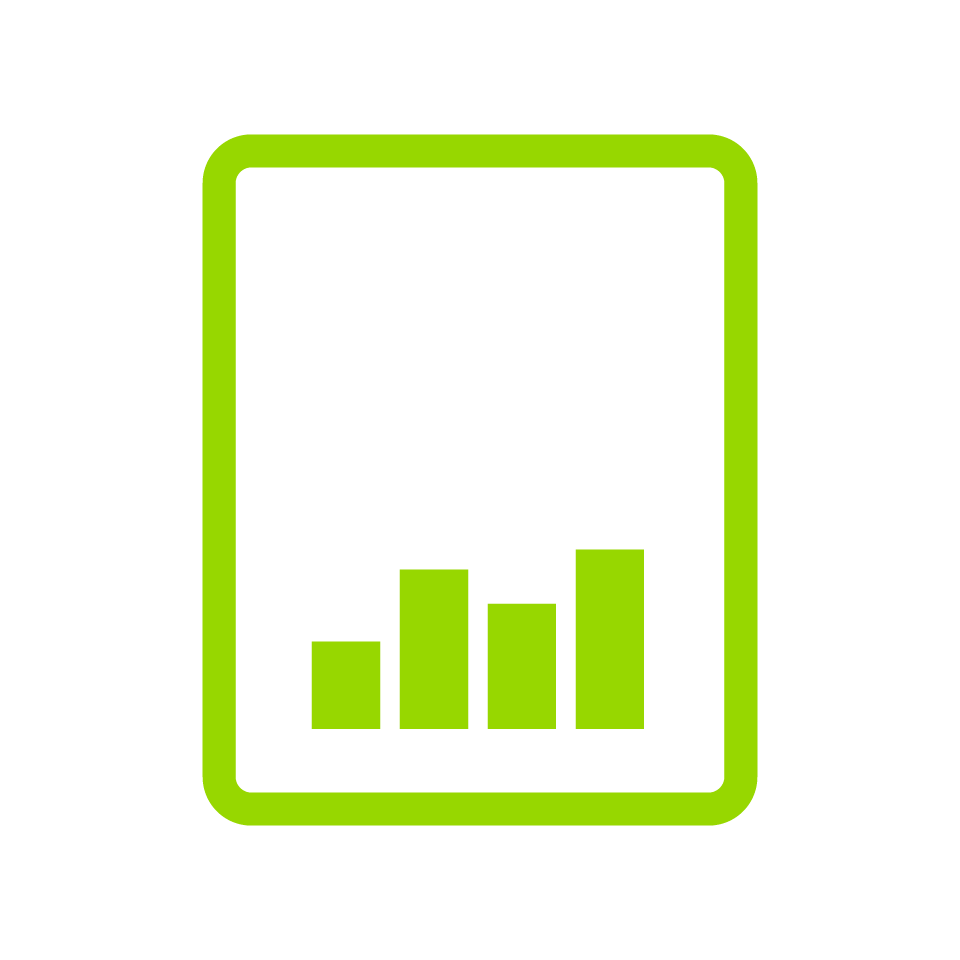
Published: 03/02/2022
UK’s biggest opportunity from battery waste is to feed its cathode manufacturing industry
Recovering battery materials is critical to making new batteries and can be produced at a lower carbon footprint than mined materials.